Webinars
This page is for researching eligibility assessments.
*We are not responsible for any misinterpretation of the text.
This document is subject to revision without notice.
In GMP, there is a special term called “Qualification” (Qualification), which is not used in other industries. Generally, qualification is performed for validation of GMP hardware, such as structural equipment. To make it easier to understand, “process validation” is performed for both “GMP hardware” and “GMP software,” while “qualification” is performed for “GMP hardware.
So what exactly is an “eligibility assessment”?
The “Guidelines for Active Pharmaceutical Ingredients GMP” glossary, which includes the following definitions.
validation
A written program that provides a high degree of assurance that a particular process, method or system will consistently deliver results that meet predetermined criteria.
eligibility assessment
The activity of demonstrating and documenting that equipment or ancillary systems are properly installed, operate correctly, and actually produce the expected results. Although qualification is part of validation, an individual qualification step alone does not constitute process validation.
This means that the validation activity includes a qualification assessment.
“Guidelines for Active Pharmaceutical Ingredients GMP” 12.30″ states the following regarding “qualification assessment.
12.30 Before beginning any process validation work, a qualification of critical equipment and ancillary facilities should be completed. Qualification is typically performed individually or in combination with the following tasks
Design-Qualification (DQ): to verify and document that the facility, equipment, or system is appropriate for its intended use.
Equipment Installation Qualification (IQ): Verify and document that the installed or upgraded equipment or system is consistent with the approved design and manufacturer’s requirements.
Operational Qualification (OQ): Verify and document that the installed or upgraded equipment or system operates as intended within its expected operating range.
Performance Qualification (PQ): Verify and document that the equipment and associated ancillary equipment and systems can function effectively and reproducibly in accordance with approved manufacturing methods and standards.
In other words, the eligibility assessment is,
DQ (Design Qualification)
IQ (Installation Qualification)
Operation Qualification (OQ)
Performance Qualification (PQ)
The DQ consists of the following. However, the “Validation Standard” is not clear about the DQ.
The statement “Complete qualification of critical equipment and ancillary facilities before beginning process validation work” indicates that qualification is a prerequisite for process validation. However, since the phrase “critical equipment and ancillary facilities” refers to “critical equipment and ancillary facilities,” the qualification of structural facilities and other GMP hardware is covered. Structural facilities (equipment and ancillary facilities) here are general and not necessarily computer-controlled (i.e., computerized systems). For example, it includes items such as centrifuges that are not computer-controlled, i.e., not equipped with software.
In addition, 5.41 of the “Guidelines for GMP for Active Pharmaceutical Ingredients” states the following
5.41 Computer hardware and software shall be demonstrated to be fit to perform the tasks imposed by appropriate installation qualification and operational qualification.
In other words, when performing qualification, which is a prerequisite for process validation, for computerized structural facilities, Installation Qualification (IQ) and Operational Qualification (OQ) must be performed. Performance Qualification (PQ) should be performed in conjunction with process validation.
Furthermore, 5.42 of the “Guidelines for GMP for Active Pharmaceutical Ingredients” states the following
5.42 The same level of testing is not required for commercially available software that has already been qualified. In addition, existing systems that have not been validated at the time of installation may be verified through retrospective validation, if appropriate documented records are available.
In other words, for commercially available software, etc., there is no need to repeat the equivalent work on the part of the pharmaceutical company, since the supplier in question has already guaranteed the quality.
Qualification is a regulation specific to pharmaceutical companies, and even if, for example, a chemical or food company were to introduce a similar structural facility, it would not perform a qualification. In other words, qualification is, so to speak, a quality assurance on top of quality assurance. Therefore, qualification is only performed for factors that directly affect product quality and are important. In other words, the factors with high risk are checked just to be sure. (See figure ? (See figure ?).
It is to perform DQ in the design phase, IQ in the fabrication and construction phase, and OQ and PQ in the testing, inspection, and commissioning phase.
Eligibility Assessment Objectives
Installation Qualification (IQ)
IQ is the initial qualification process to ensure that the equipment has the required and expected service content. In Japanese, it is called Installation Qualification.
The purpose of IQ is to verify that GMP hardware, such as structural equipment, has been installed correctly.
The IQ primarily evaluates the following, although some actions may be performed in-house by the supplier The manufacturer (pharmaceutical company) is responsible for evaluating, challenging, testing, etc., whether the equipment is suitable for use.
Equipment design summary (enumeration of IQ considerations)
Installation conditions
Calibration, preventive maintenance, cleaning schedules
Safety Overview
Supplier documents, prints, drawings and manuals
Software Documentation
Spare Parts List
environmental condition
Operational Qualification (OQ)
OQ is the process of proving that a process produces acceptable results and establishes limits (worst case). In Japanese, it is called Operational Qualification.
The purpose of OQ is to challenge (preliminarily test) process parameters to assure that the product can be manufactured to meet the requirements by conducting tests to determine manufacturing conditions, such as worst-case testing.
By implementing OQ, the various action levels of the manufacturing process can be known and maintained in a state of control according to product characteristics. This leads to process robustness.
The OQ will primarily assess the following
process control limit
Software Parameters
Raw material specifications
process operating procedure
Material Handling Requirements
Process Change Management
Training (education to give OQ the skills to be able to do OQ)
Short-term stability and process capability (process capacity)
Failure Mode Effects, Action Levels and Worst Case Conditions (Failure Mode Effects Analysis: FMEA, Fault Tree Analysis: FTA)
Statistical validation techniques such as screening experiments and design of experiments to idealize the process can be used to make key process parameters available during this phase.
Performance Qualification (PQ)
PQ is the process of establishing the stability of a process over time. In Japanese, it is called performance qualification.
The purpose of PQ is to verify that the process is capable of producing, on a permanent basis, products that pass specifications under normal operating conditions. In other words, PQ manufactures products under the actual production conditions established in OQ. At the same time, the various action levels and the contents of the standard operating procedures (SOPs) that contain them are verified, and the process is further assured through repeated challenge tests.
The PQ will primarily evaluate the following
Actual product and process parameters and methods established by OQ
Acceptability of product standards
Guarantee of process capability established by OQ
Process reproducibility (repeatability), long-term process stability
Product and process data should be analyzed to determine the normal range of variation within which the output of the process is within specifications.
Knowing the normal range of variation will clarify whether it is in a controlled state or within a certain tolerance to be able to produce a specific output. Reducing and controlling the range of variation provides a high degree of quality assurance. (See Figures 4-6)
The variables to be controlled depend on the characteristics and subtleties of the process, but are as follows
Temperature/humidity/equipment exterior/condensation
Fluctuation/vibration/light on power supply
Environmental contamination/process water purity/human factors
Different brands of raw materials
Viscosity variation of raw solution due to raw material lot switching (affects product removal rate performance)
Difference between CSV and Process Validation (PV)
When the author conducts seminars, a question he often receives is, “What is the difference between process validation (hereafter PV) and CSV?
In other words, the question is what is the difference between DQ, IQ, OQ, and PQ in PV and DQ, IQ, OQ, and PQ in CSV?
The “Guidelines for the Appropriate Management of Computerized Systems at Manufacturers and Distributors of Pharmaceuticals and Quasi-Drugs” (Pharmaceutical and Food Safety Bureau, Ministry of Health, Labour and Welfare, No. 1021/11, dated October 21, 2010, Notification of the Director, Monitoring, Guidance and Narcotics Control Division, Pharmaceutical and Food Safety Bureau, Ministry of Health, Labour and Welfare. The “New Guideline”) seems to confuse PV and CSV in structural facilities.
Process validation (PV) is performed on GMP hardware + GMP software. Qualification is performed on the GMP hardware. In this case, GMP hardware consists of hardware and software.
Systems controlled by software (including firmware and PLCs) are called computerized systems. Computerized systems must implement CSV. In other words, they must implement software quality assurance.
To begin with, computerized system validation (CSV) is a qualification of GMP hardware (structural equipment and support systems).
PV, on the other hand, verifies GMP hardware and GMP software (e.g., workers, raw materials and supplies, manufacturing and operating methods, cleaning and other operations).
The PQ of CSV is to verify that the actual equipment meets the user requirement specifications, which is clear from the V-Model.
The PQ for PV is to verify the stability of the process by actually producing at least three lots using actual equipment.
Incidentally, the reason for conducting the survey in three or more lots is that the directness of the process is not known with respect to fluctuations in quality, etc., in two lots.
The ability of the process to consistently produce products that pass specifications under normal operating conditions is the objective of PQ in PV.
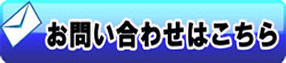
【related product】
VOD Distribution Seminar
There is no limit to the number of times or duration of viewing our VOD-delivered seminars.
You can watch it over and over again at your favorite time.
■Learn the essentials in 180 minutes] Revised GMP Seminar Series – Validation
■ (Total 5 Courses) [Learn the Essentials in 180 Minutes] Revised GMP Seminar Series [One-Time Course
■ Japan’s easiest-to-understand [super-introductory] seminar on the revised GMP Ministerial Ordinance
■ Seminar on Key Points of Revised GMP Ordinance
■ Response to “Supplier Management of Raw Materials, etc.” in the Revision of the GMP Ministerial Ordinance
Seminar Video
You will receive an email with the URL to download the materials and seminar video.
DVDs will be mailed separately.
■[Seminar Video] [Learn the Essentials in 180 Minutes] Revised GMP Seminar Series Validation Edition.
■[Seminar Video] (5 Courses) [Learn the Essentials in 180 Minutes] Revised GMP Seminar Series (5 courses in total)
■ Japan’s easiest-to-understand [super-introductory] seminar on the revised GMP Ministerial Ordinance
■ Seminar on Key Points of Revised GMP Ordinance
■ Response to “Supplier Management of Raw Materials, etc.” in the Revision of the GMP Ministerial Ordinance
]]>
You can certainly see your enthusiasm in the article
you write. The arena hopes for more passionate writers like you who aren’t afraid to say how they believe.
All the time follow your heart.
At this time I am ready to do my breakfast, after having my breakfast coming again to read more news.