Why is an audit necessary?
So far, we have explained quality control (QC) and quality assurance (QA).
In this issue, I would like to discuss why audits are necessary.
The reasons for the need for the audit are as follows
1.Nothing that man makes is perfect in every way (it always contains imperfections).
2.There are parts of the world that I cannot find on my own.
3.We all have our weaknesses, and sometimes devious thoughts, including ill-conceived ones, rear their ugly heads.
Auditing is a third-party verification process and is an essential part of quality assurance. However, it is not the job of the auditor to find defects. Its primary task is to confirm that there are no defects.
For example, let’s say we find a posting error or calculation error in an audit. In such a case, what is appropriate to point out?
The author would say, “If transcription and calculation errors are left unchecked until the audit, it can be said that quality control (QC) is not thorough and quality assurance (QA) is not functioning. Therefore, the relevant QMS should be revised to improve them and prevent their recurrence. The report points out that
In other words, it does not point out the errors themselves, such as transcription errors or calculation errors, but rather the defects in the system (QMS: Quality Management System) that allow these errors to remain undetected and unchecked.
In the worst cases, we have seen audit reports that point out only the “te-ni-ho” of the text, which is not the end of the story. Correcting the writing style of a document does not guarantee quality assurance.
Of course, it is necessary to point out any defects that may be found.
It is also necessary to express deterrence against devious ideas and to take a firm stand in case of emergency.
Audit Personnel Requirements
The person in charge of the audit must be a third party with no vested interest in the audited department.
For example, it does not matter if the project is delayed or costs are incurred! A third party is not a third party if he or she is not concerned if the project is delayed or costs are incurred. A third party is not a third party if he or she is also troubled if the project is delayed or costs are increased.
However, even disinterested third parties are colleagues. How can we expect to persuade customers or regulators with documents and records that do not persuade our colleagues?
The auditor must observe things from a third-party perspective, logically identify inconsistencies, problems, and issues, determine their causes, and propose solutions.
In other words, the audit personnel must be in-house consultants.
For this purpose, the person in charge of the audit must be experienced in the relevant business. This is because it is impossible to point out deficiencies or identify risks in a QMS for work that has not been done before.
Conformity and Validity
In ISO 9000 “Quality Management Systems – Fundamentals and Terminology”, the terms conformity and adequacy are defined. Conformity verification refers to the investigation of whether a company’s QMS complies with regulatory requirements and international standards. Validation refers to the investigation of whether the conforming QMS is consistent with the implementation records.
FDA inspections are to use 25% of the time for conformity checks and 75% of the time for validity checks. Thus, in FDA inspections, the records are examined after the QMS investigation is conducted. In other words, top-down inspections are the mainstream. In contrast, most audits in Japan and Europe are bottom-up inspections, in which as much as 90% of the time is spent on the investigation of records, and when there is a question in the records, the QMS concerned is checked.
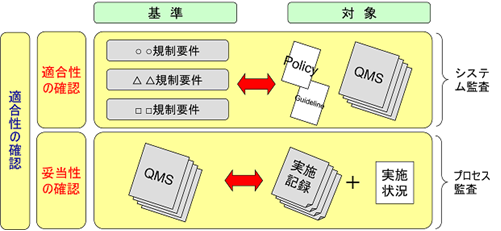
Comment