Which companies are subject to FDA inspections
One of the questions I am often asked is, “What types of companies are subject to routine FDA inspections?” One of the questions I am often asked is, “What types of companies are subject to routine FDA inspections? In the case of the FDA, the site selection model (SSM) is used. The FDA uses the SSM to calculate a score for all sites in the catalog using risk-based factors.
- Product-specific risks
Different types of products have different levels of risk based on characteristics such as dosage form, route of administration, or whether the product is intended to be sterile. For example, a manufacturing facility that produces a sterile injectable drug product will have a higher inherent product risk than a facility that produces oral capsules. - Facility Type
The level of risk depends on the operations the facility performs. Facilities that manufacture pharmaceuticals or active ingredients are at higher risk than facilities that package only pharmaceuticals. - Patient exposure
The more products a facility manufactures, the more likely patients are to encounter products manufactured at that facility. This refers to both the number and type of products manufactured. A facility that manufactures many products will have a higher exposure factor than a facility that manufactures few products. - inspection history
Facilities that do not meet the quality standards established at the time of a previous inspection are considered higher risk than those that have met the standards in the past. - Time since last inspection
As the time since the facility was last inspected increases, the risk that it may not meet established quality standards increases, as does the need for re-inspection. - hazard signal
Events such as product recalls and manufacturer or patient reports of facility-related quality problems result in higher risk scores compared to facilities with few or no major hazard signals.
The FDA uses such a site selection model (SSM) to determine which facilities to inspect.
Periodic inspections of manufacturing facilities by the FDA were originally stipulated in the FDC Act to be conducted once every two to three years.
However, the FDA cannot increase the number of inspectors very much. Even within the U.S. alone, it is no longer possible to conduct an inspection every two or three years. Nevertheless, supply chains have become globalized, and inspections must now be conducted in Japan, Europe, China, India, and many other countries.
As a result, it is no longer possible to perform the periodic inspections every two to three years, as required by the FDC Act.
Therefore, around 2003, the FDC Act was amended to require inspections to be conducted on a risk basis, rather than every two to three years.
The resulting method was to select inspection targets according to SSM scores.
Since 2015, the FDA has moved to a program of conducting foreign drug inspections rather than domestic. While domestic in the U.S. is of course important, the supply chain has become globalized and drugs, including APIs, are increasingly imported from foreign countries. Therefore, it has increased the number of foreign companies and foreign inspections.
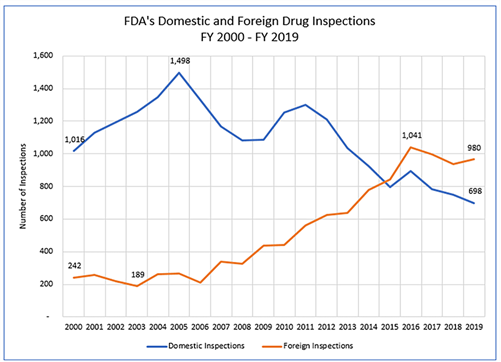
Comment