DHF Principles
In this article, I would like to explain how to manage DHF. This is because most medical device companies have the wrong way to manage DHFs.
In most medical device companies that the author has experienced, each design document is often bound in a binder. This management method is a mistake.
Why DHF is needed
FDA’s 21 CFR 820 QSR requires the creation of a Design History File (DHF) in design controls; in ISO 13485, it is called a Design Development File.
As the name suggests, the DHF is a filing of the design history.
The reason why a DHF is necessary is that the design of the same product may have changed between one that was shipped five years ago, one that was shipped three years ago, and one that is currently being shipped.
For example, suppose a repair request is received due to a failure of a product. If the product was shipped five years ago, it would be difficult to investigate the cause of the failure unless a complete set of design documents from that time can be promptly retrieved.
Thus, the DHF should file all the design documents at the time of each design change in a horizontal skewer. In other words, it is like taking a snapshot of the latest design documents at that time.
How FDA requires DHF to be managed
Below are the documentation requirements for DHFs in FDA QSRs.
820.30 Design Management
(e) Design Review
Each manufacturer shall establish and maintain procedures to ensure that design reviews with formally documented design results are planned and conducted at the appropriate stage of equipment development. This procedure shall ensure that the participants in each design review include the following This procedure is to ensure that each design review participant includes: a representative of all functions related to the design phase being reviewed, a person or persons not directly responsible for the design phase being reviewed, and, if necessary, an expert. Documenting the results of the design review, e.g., identifying the design, date, and the person(s) who reviewed it, in the Design History File (DHF).
(f) design verification
Each manufacturer shall establish and maintain procedures and verify equipment designs. Design verification is to ensure that the output from the design meets the requirements of the inputs to the design. The results of the design verification, e.g., identifying the design method, date, and the person(s) who performed the verification, shall be documented in the design history file (DHF).
(g) Design validation
Each manufacturer shall establish and maintain procedures and perform design validation. Design validation shall be performed on units, lots, or batches of initial production or similar objects under defined operating procedures. Design validation shall include testing of the manufactured unit under actual or simulated conditions of use to ensure that the equipment meets defined user needs and intended uses. Design validation shall include software validation and hazard analysis where appropriate. The results of the design validation, e.g., identifying the design method, date, and person(s) who performed the validation, shall be documented in the design history file (DHF).
In other words, in the FDA QSR, there are three design documents that must be documented in the DHF
- Results of Design Review
- Results of Design Verification (Design Verification)
- Results of Design Validation
However, in many medical device companies, the results of Design Verification and Design Validation will always be input into Design Review.
In other words, it can be understood that the FDA QSR requirement is to file the results of the design review in the DHF.
For a given product, the design review will proceed from DR0 to DR1 to DR2 to DR3, and so on.
The DHF files all the design documents and results of the design review process in a single document (i.e., a snapshot).
Since design reviews are generally set at the end of each phase of design development (i.e., they are reviews to transition phases), filing the complete set of design review results in the DHF will ensure that the design control history is properly documented.
The DHF does not have to be physically stored. For example, if the drawings are maintained in CAD or other data, it is acceptable as long as they refer to an electronic record storage location.
In other words, the DHF may be maintained as an inventory and the design documents may be kept in a separate binder or electronic record. Importantly, the then-current version (edition) should be promptly retrievable as the design development progresses.
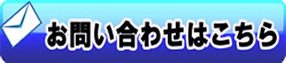
Comment