Management of unsuitable goods
In this article, I would like to discuss the management of nonconforming products in medical device manufacturing. First, it is important to note that nonconforming and nonconforming products are different.
- Nonconformity refers to the failure to meet the specified requirements.
- Nonconformity Product is a product that does not meet specified requirements (specifications).
ISO 13485 “8.3 Control of nonconforming products” is divided into “8.3.2 Actions on nonconforming products before delivery” and “8.3.3 Actions on nonconforming products found after delivery”.
In this issue, the former “8.3 Control of Nonconforming Products” will be explained.
8.3.2 Actions to be taken on non-conforming products prior to delivery
The organization handles nonconforming product in one or more of the following ways
a) Take action to remove any nonconformities found.
b) Take steps that prevent the original intended use or application of the product.
c) By special adoption, formal permission is granted to use, release or determine that it has passed.
Ensure that the organization accepts nonconforming products by special adoption only if justification is provided, approval is obtained, and applicable regulatory requirements are met.
Records identifying persons accepted through special recruitment and persons authorized for special recruitment shall be maintained (see 4.2.5).
For nonconforming products that occur before delivery, i.e., during manufacturing, one of the following three actions must be taken
- Take action to remove any nonconformities found. (Rework)
- Take steps to ensure that the product cannot be used or applied as originally intended. (Discard)
- By Special Adoption, formal permission is granted to use, release or determine that it has passed. (Special Adoption)
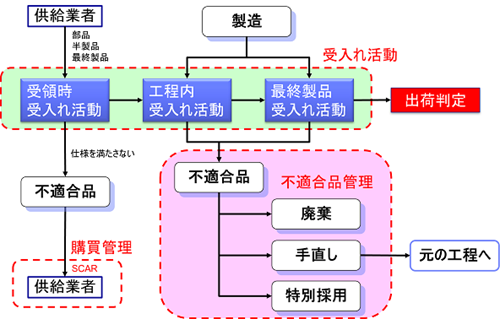
Rework (rework)
When nonconforming products are found in the manufacturing process, they may be reworked, i.e., manufactured again. ISO 13485 “8.3.4 Rework” has the following requirements
8.3.4 modification
Modifications shall be performed in accordance with documented procedures that take into account the potential The rework is performed according to a documented procedure that takes into account the potential negative impact of the rework on the product.
This procedure is issued based on the same review and approval as the original procedure.
After completion of the rework, the product is verified to ensure that it complies with applicable acceptance criteria and regulatory requirements.
A record of rework is maintained (see 4.2.5).
In the author’s audits of medical device companies, he often sees companies conducting rework without written procedures. This is a violation of regulatory requirements. Rework procedures must be written for each non-conforming product and must include “removal procedures,” “reassembly procedures,” “additional inspection procedures,” etc. In other words, it must not be removed without a written procedure. In addition, once assembled components are removed and reassembled, there is a possibility of damaging the equipment. Therefore, in addition to normal inspections, necessary inspection procedures must be performed. These procedures must be reviewed, approved, and issued by the same person who prepared the manufacturing procedures.
disposal
For example, if a purchased part or other item is found to be non-conforming at the receiving inspection, it should not be placed on the line and should be discarded or returned to the supplier concerned. In addition, some equipment may be disposed of rather than reworked if it is non-conforming at final inspection.
special recruitment
In medical devices, special adoption is applicable only when the customer agrees (customer requirements are met) and regulatory requirements are met.
In the course of the author’s consultations and audits, he has seen cases of repeated special hires. Repeated special hires due to the same problem are not allowed. (However, regulatory requirements, etc. do not specify that repeated special hires are not allowed.)
Common sense would dictate that the special hiring process be repeated,
They despise design standards.
Failure to improve the manufacturing process.
This is because either or both of the following are true.
To avoid having to implement special hiring again,
relax design standards
Implement CAPA to prevent recurrence
One of the following measures must be taken. In general, design criteria must be narrower than customer requirement criteria and manufacturing criteria must be narrower than design criteria.
Comment