Inspection upon receipt from supplier
Last time we discussed non-conforming product management.
The three principles in manufacturing, not limited to medical devices, are: do not let defects in, do not let them flow in, and do not let them out.
In this issue, we would like to examine the incoming inspection of parts, etc. from suppliers (receiving inspection). As shown in the figure, receiving inspection is distinguished into receiving inspection, intermediate inspection, and final inspection.
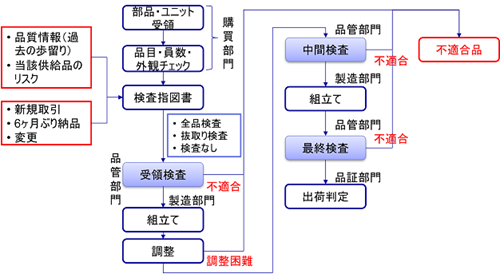
In the author’s experience, many companies skip the receiving inspection (inspection upon receipt from the supplier) and remove the relevant parts when a defect or other problem is found in the process.
This makes it unclear whether the originally purchased parts were defective or whether they were broken during the assembly process.
It also takes time and effort to rework.
While there are problems with not conducting receiving inspections at all, on the other hand, receiving inspections themselves are also time-consuming and costly. Especially for parts purchased in large quantities, it is difficult to inspect all products.
Therefore, it is desirable to conduct receipt inspections at the appropriate level.
100% inspection
The first items that must be fully inspected are critical safety components (e.g., laser sources, lenses, etc.) and labels/labeling.
A critical safety component is one whose quality failure leads to a quality failure of the entire product, or more specifically, one that affects the safety of patients and users.
In other words, depending on the risk of the supplies in question, a full inspection must be conducted.
In addition, labels and labeling (instruction manuals, attachments, etc.) may be visually inspected, and all products must be inspected.
The FDA requires “label/labeling integrity”. This is because in the unlikely event that a label or labeling has a problem or is unreadable, it will have a direct impact on safety.
On the other hand, there are some items that do not necessarily need to be inspected in their entirety, but should be inspected by sampling.
What is 3H?
3H is an acronym for “first time,” “henkou,” and “hishikari. First-time traders may want to set the AQL inspection level to “tight inspection”. Similarly, it may be a good idea to set the AQL inspection level to “tight inspection” for parts that have just been changed, or for vendors with whom you have a business relationship but have not purchased for a long time.
Dynamic inspection level changes
It is also important to dynamically change the inspection level of the AQL to “loose” or “tight” inspection based on historical yield data.
If the supplier’s performance is good, there is no need to use its own time, effort, and cost to conduct receiving inspections.
In such cases, consideration should be given to setting the AQL inspection level to “loose inspection”.
Also, “no inspection” may be acceptable for low-risk parts (e.g., screws) or when the supplier’s performance is extremely high. Thus, it is desirable to inspect the receipt of purchased parts, etc. at a level appropriate to the risk and the supplier’s performance.
Comment