Action Limits and Alert Levels
Action limits and alert levels are used, for example, as criteria to control microbial or suspended particle limits.
The action limit, or action range limit, is the limit of the permissible operating range, which, if exceeded, constitutes a deviation. In such cases, appropriate investigation and corrective measures based on the investigation must be implemented.
The Alert level is the alert area limit width, within which the normal operating range is located.
Alert levels are early warnings of potential deviations from normal operating conditions and validated states. Exceeding an alert level does not necessarily require corrective action, but it does require appropriate scrutiny and follow-up, or preventive action, to address potential problems.
Alert levels are set based on periodic eligibility validation trend data and are reviewed periodically. Alert levels can be based on a number of parameters, such as adverse trends, individual transient deviations (excursions) that exceed set limits, recurring events, etc.
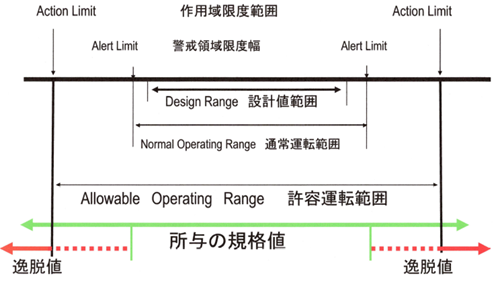
For example, consider the temperature control of a refrigerator (2°C to 8°C). In most cases, the temperature setting of a refrigerator is supposed to be 5°C. This is to prevent the temperature from temporarily rising or falling and deviating when the door is opened. This is to prevent the temperature from temporarily rising or falling and deviating when the door is opened.
Let’s say the alert level is set between 3°C and 7°C. In this case, the alert level would be set to 5°C again when the alert level is exceeded or when the trend is moving in the direction of deviation. This is preventive action.
If the temperature exceeds the alert level or is heading in the direction of deviation, a problem may be lurking somewhere.
For example, the refrigerator door may no longer close properly, there may be a gap, or the door may be opened and closed too often.
Since it is not yet a deviation, no corrective action is required, but preventive action is needed to avoid deviation.
transient deviation(Excursion)and temporary deviations(Spike)
A transient deviation is a deviation of relatively short duration (e.g., 20 minutes or less).
Also, a temporary deviation is a deviation only for a brief moment (e.g., one minute).
Some companies allow transient or primary deviations and do not take them up as deviations unless they exceed the prescribed time.
However, alert-level transient deviations should be documented and reviewed and should include an investigation to determine if the transient deviation is a single (isolated) event or if the result indicates a bad trend or system degradation.
This means that each action limit transitory deviation should be investigated to determine possible root causes and potential impacts on product quality and manufacturing processes.
related product
[blogcard url=https://xn--2lwu4a.jp/qms-rx/ title=”QMS(手順書)ひな形 医薬品関連” ] [blogcard url= https://ecompliance.co.jp/SHOP/P130.html title=”【書籍】 査察指摘事例をふまえた 医薬品の試験検査室/製造工程における OOS/OOT調査・手順と事例考察”] [blogcard url= https://ecompliance.co.jp/SHOP/QMS-MHLW-16.html title=”【2021年度改正QMS省令対応】是正処置/予防処置規程・手順書・様式”] [blogcard url= https://ecompliance.co.jp/SHOP/EB009_EB009a.html title=”【書籍】微生物の創薬への応用とGMPに対応した環境微生物管理”] [blogcard url= https://ecompliance.co.jp/SHOP/L_CAPA.html title=”【VOD】製薬企業・医療機器企業におけるFDAが要求するCAPA導入の留意点”]]]>
Comment